5 Proven Ways Manufacturers Can Get Started With Analytics
By TheWAY - 11월 15, 2019
ISTOCK
- 46% of manufacturers agree that implementing and using data analytics is necessary to stay competitive and grow their businesses.
- 69% of manufacturing decision-makers believe analytics will be crucial for business success in 2020, with 15% considering it crucial today.
- 32% of manufacturers see the potential for analytics to improve supply chain performance and increase revenue. Manufacturers perceive data analytics as a key component of successful sourcing, procurement, and production strategies.
Going into 2020, manufacturers are at an inflection point in their adoption of analytics and business intelligence (BI). Analytics applications and tools make it possible for them to gain greater insights from the massive amount of data they produce every day. And with manufacturing leading all industries on the planet when it comes to the amount of data generated from operations daily, the potential to improve shop floor productivity has never been more within reach for those adopting analytics and BI applications.
Analytics and BI Are High Priorities In Manufacturing Today
Increasing the yield rates and quality levels for each shop floor, machine and work center is a high priority for manufacturers today. Add to that the pressure to stay flexible and take on configure-to-order and engineer-to-order special products fulfilled through short-notice production runs and the need for more insight into how each phase of production can be improved. Gartner’s latest survey of heavy manufacturing CIOs in the 2019 CIO Agenda: Heavy Manufacturing, Industry Insights, by Dr. Marc Halpern. October, 15 2018 (Gartner subscription required) reflects the reality all manufacturers are dealing with today. I believe they’re in a tough situation with customers wanting short-notice production time while supply chains often needing to be redesigned to reduce or eliminate tariffs. They’re turning to analytics to gain the insights they need to take on these challenges and more. The graphic below is from Gartner’s latest survey of heavy manufacturing CIOs, it indicates the technology ares where heavy manufacturing CIOs’ organizations will be spending the largest amount of new or additional funding in 2019 as well as the technology areas where their organizations will be reducing funding by the highest amount in 2019 compared with 2018:
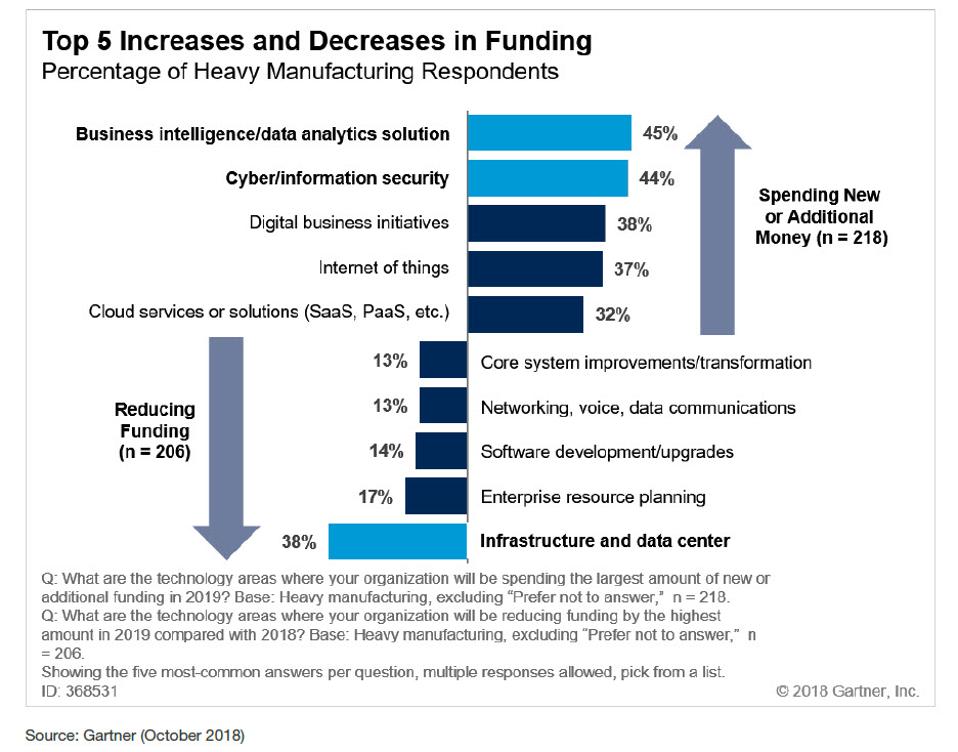
SOURCE: GARTNER, "2019 CIO AGENDA: HEAVY MANUFACTURING, INDUSTRY INSIGHTS," DR. MARC HALPERN. OCTOBER, 15 2018 (GARTNER SUBSCRIPTION REQUIRED)
Knowing Which Problems To Solve With Analytics
Manufacturers getting the most value from analytics start with a solid business case first, based on a known problem they’ve been trying to solve either in their supply chains, production or fulfillment operations. The manufacturers I’ve worked with focus on how to get more orders produced in less time while gaining greater visibility across production operations. They’re all under pressure to stay in compliance with customers and regulatory reporting; in many cases needing to ship product quality data with each order and host over 60 to 70 audits a year from customers in their plants. Analytics is becoming popular because it automates the drudgery of reporting that would otherwise take IT team’s days or weeks to do manually.
As one CIO put it as we walked his shop floor, “we’re using analytics to do the heavy data crunching when we’re hosting customer audits so we can put our quality engineers to work raising the bar of product excellence instead of having them run reports for a week.” As we walked the shop floor he explained how dashboards are tailored to each role in manufacturing, and the flat screen monitors provide real-time data on how five key areas of performance are doing. Like many other CIOs facing the challenge of improving production efficiency and quality, he’s relying on the five core metrics below in the initial roll-out of analytics across manufacturing operations, finance, accounting, supply chain management, procurement, and service:
- Manufacturing Cycle Time – One of the most popular metrics in manufacturing, Cycle Time quantifies the amount of elapsed time from when an order is placed until the product is manufactured and entered into finished goods inventory. Cycle times vary by segment of the manufacturing industry, size of manufacturing operation, global location and relative stability of supply chains supporting operations. Real-time integration, applying Six Sigma to know process bottlenecks, and re-engineering systems to be more customer-focused improve this metrics’ performance. Cycle Time is a predictor of the future of manufacturing as this metric captures improvement made across systems and processes immediately.
- Supplier Inbound Quality Levels - Measuring the dimensions of how effective a given supplier is at consistently meeting a high level of product quality and on-time delivery is valuable in orchestrating a stable supply chain. Inbound quality levels often vary from one shipment to the next, so it’s helpful to have Statistical Process Control (SPC) charts that quantify and show the trends of quality levels over time. Nearly all manufacturers are relying on Six Sigma programs to troubleshoot specific trouble spots and problem areas of suppliers who may have wide variations in product quality in a given period. This metric is often used for ranking which suppliers are the most valuable to a factory and production network as well.
- Production Yield Rates By Product, Process, and Plant Location – Yield rates reflect how efficient a machine or entire process is in transforming raw materials into finished products. Manufacturers rely on automated and manually-based approaches to capture this metric, with the latest generation of industrial machinery capable of producing its yield rate levels over time. Process-related manufacturers rely on this metric to manage every production run they do. Microprocessors, semiconductors, and integrated circuit manufacturers are continually monitoring yield rates to determine how they are progressing against plans and goals. Greater real-time integration, improved quality management systems, and greater supply chain quality and compliance all have a positive impact on yield rates. It’s one of the key measures of production yield as it reflects how well orchestrated entire production processes are.
- Perfect Order Performance – Perfect order performance measures how effective a manufacturer is at delivering complete, accurate, damage-free orders to customers on time. The equation that defines the perfect order Index (POI) or perfect order performance is the (Percent of orders delivered on time) * (Percent of orders complete) * (Percent of orders damage free) * (Percent of orders with accurate documentation) * 100. The majority of manufacturers are attaining a perfect order performance level of 90% or higher, according to the The American Productivity and Quality Center (APQC). The more complex the product lines, configuration options, including build-to-order, configure-to-order, and engineer-to-order, the more challenging it is to attain a high, perfect order level. Greater analytics and insights gained from real-time integration and monitoring help complex manufacturers attained higher perfect order levels over time.
- Return Material Authorization (RMA) Rate as % Of Manufacturing – The purpose of this metric is to define the percentage of products shipped to customers that are returned due to defective parts or not otherwise meeting their requirements. RMAs are a good leading indicator of potential quality problems. RMAs are also a good measure of how well integrated PLM, ERP and CRM systems, resulting in fewer product errors.
Conclusion
The manufacturers succeeding with analytics start with a compelling business case, one that has an immediate impact on the operations of their organizations. CIOs are prioritizing analytics and BI to gain greater insights and visibility across every phase of manufacturing. They’re also adopting analytics and BI to reduce the reporting drudgery their engineering, IT, and manufacturing teams are faced with as part of regular customer audits. There are also a core set of metrics manufacturers rely on to manage their business, and the five mentioned here are where many begin.
0 개의 댓글